相关推荐资讯
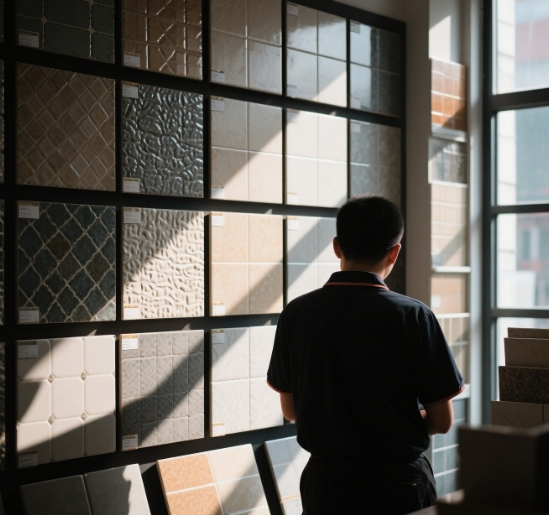
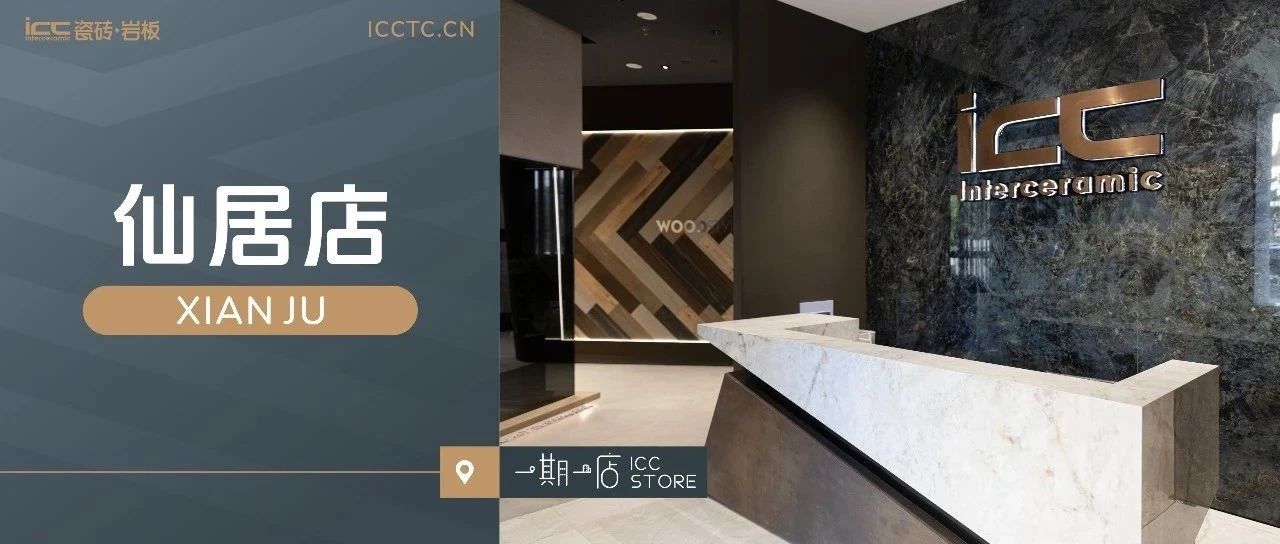
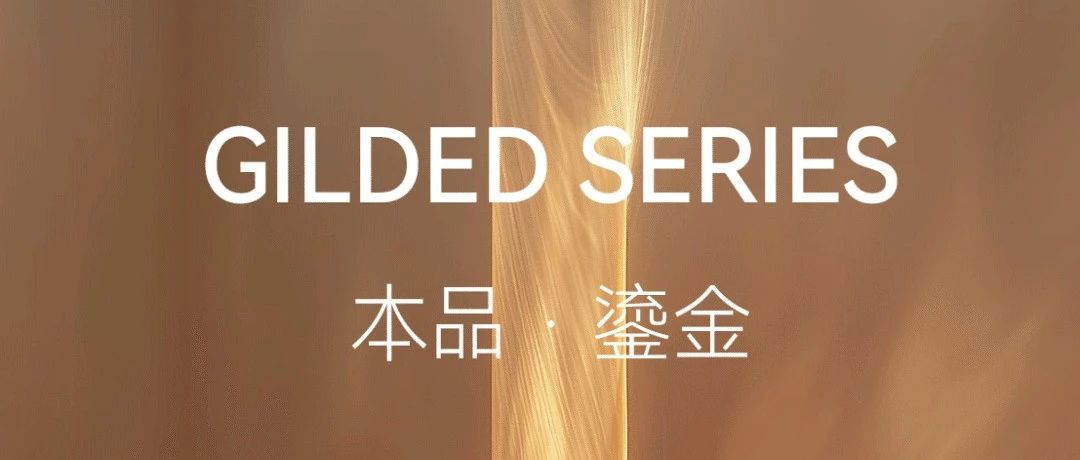

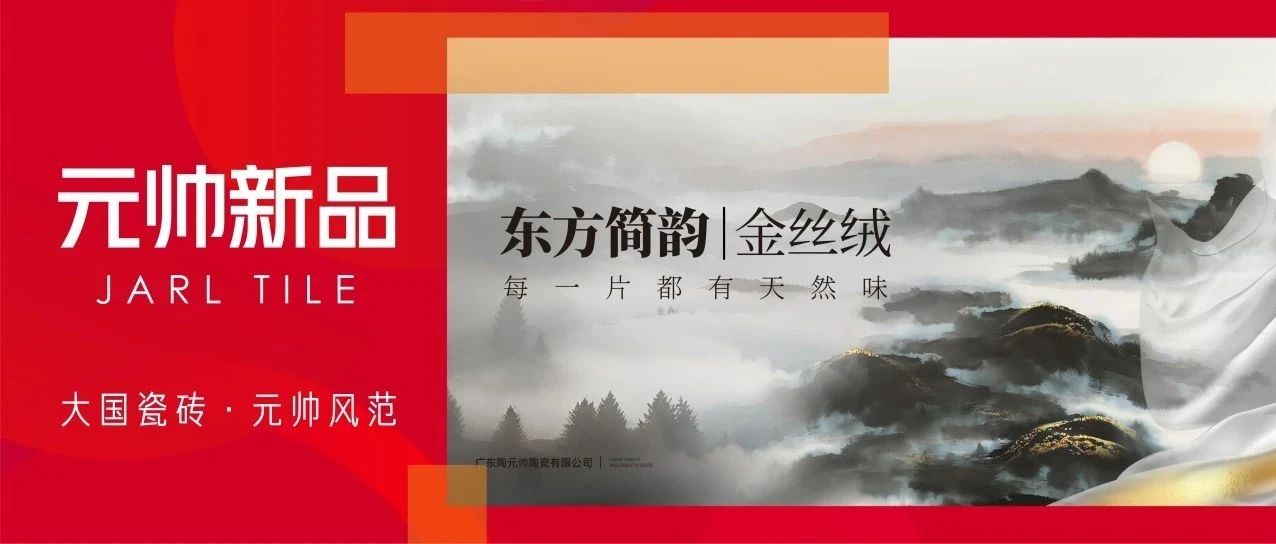
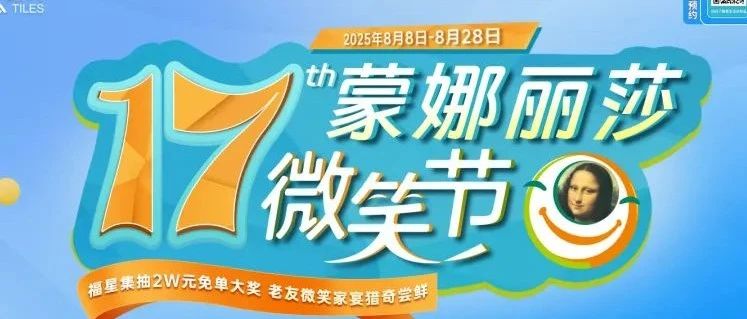
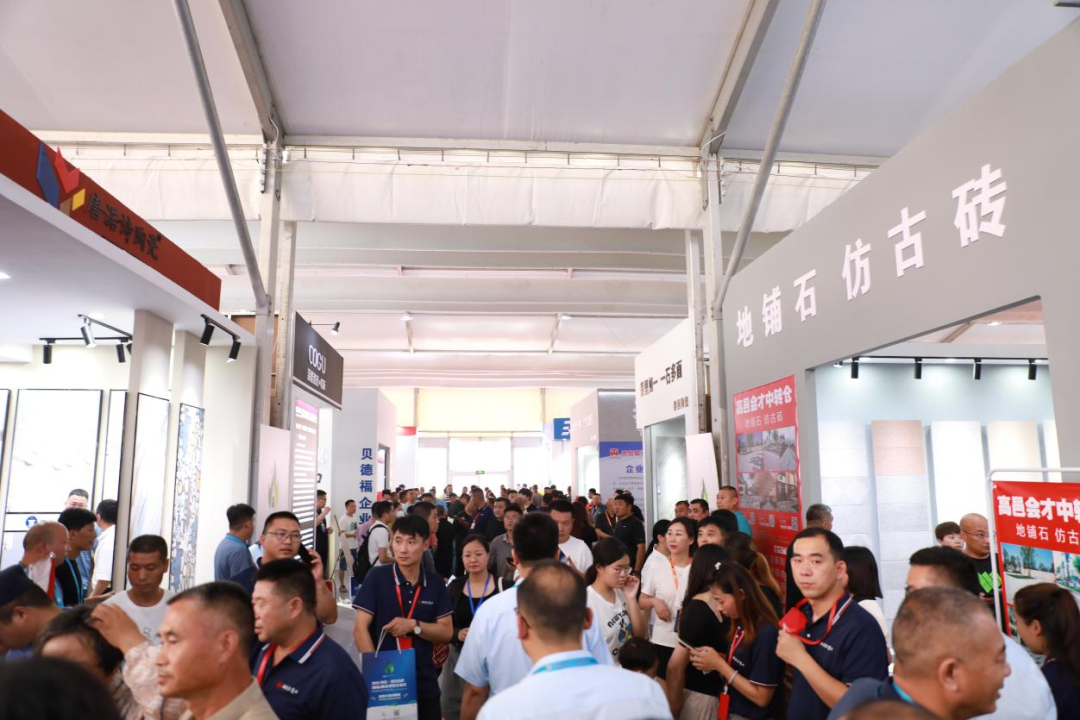
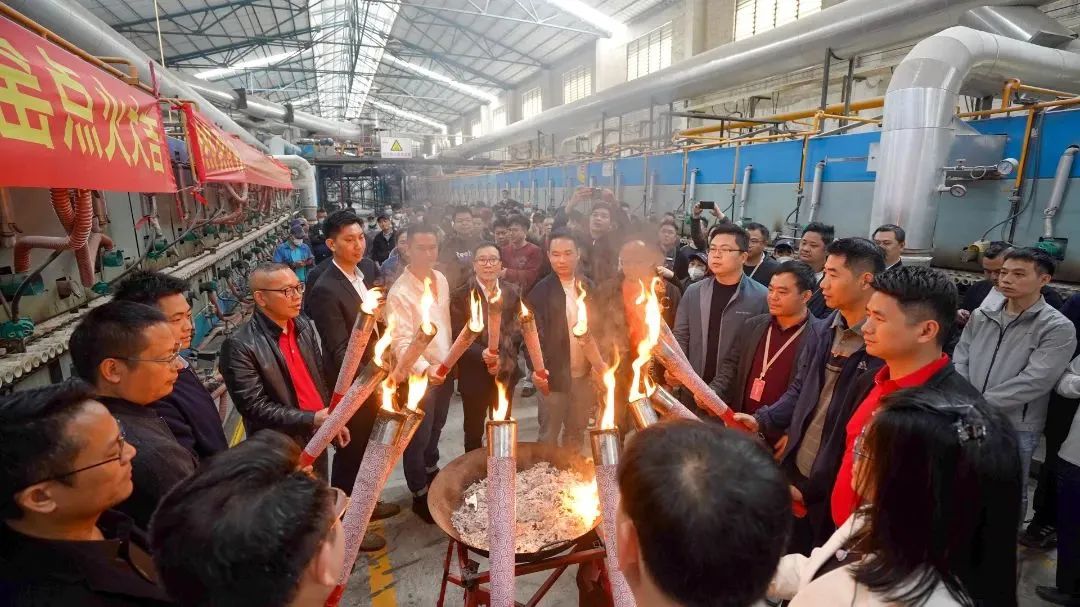
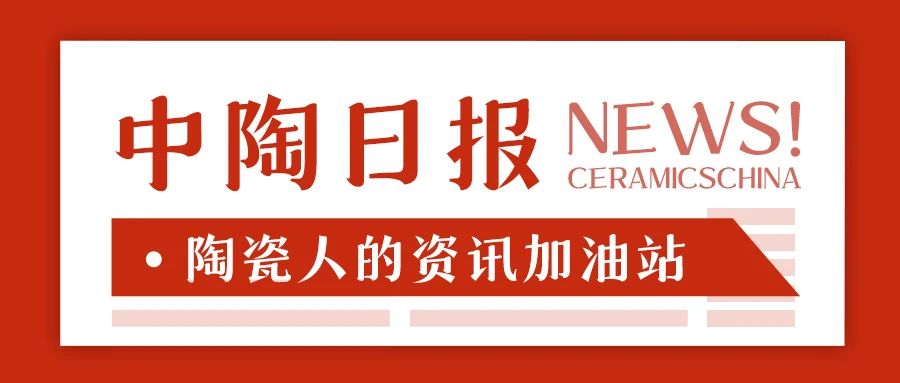
在釉面砖生产过程中经常会出现凹坑缺陷,如果控制不合理,很可能给企业带来损失。造成釉面凹坑的原因有很多,既有操作方面的原因,也有设备方面的原因,有时还会涉及到原料的问题,下面我们就来看看釉面砖产生凹坑原因及处理方法吧!
一、釉料中带有低熔点物质
1、原因
釉料中带有低熔点物质,配方中添加CMC等比例不合理,或者粒度分布粗细不均匀。有些陶瓷厂因换高岭土批次,其含水量变少,使得釉浆排气不顺而导致凹坑,透过减少配方中高岭土和CMC才得缓解,釉浆中的CMC变质、发酵也会导致淋出的凹坑。
2、处理方法
针对这种凹坑,要加强进料验收,防止低熔点物质或杂质混入,一般透过水洗原料,过200目筛看是否留下杂质;热天要防止釉中的CMC变质。应将面釉存放在阴凉处或在面釉中加入杀菌剂。
二、操作不当
1、原因
员工使用调花釉用的搅釉棍进行调釉,或者使用调花釉用比重瓶、流速杯接触釉浆,也有员工上班后未洗手直接接触釉,喷水、底釉、面釉见过添加剂,压缩空气中有油污染,这些都是造成凹坑的原因,压缩空气中有油污大多发生在检修后的空压机,这类凹坑大多数为圆型凹坑,有深有浅,位置不一。
2、处理方法
针对这种凹坑,要加强员工的操作标准化,不定期检查左中右偏差、流速等和工作桶、过筛状况等;检查储釉容器、搅拌机、釉泵、输送带和喷水、喷釉柜的压缩空气中是否有油污,必要时加适量的除油液体清洗。
三、喷水不均匀
1、原因
喷水桶有水垢或喷水后有水滴,或钟罩滴水在坯体表面,引起坯体局部釉浆干燥速度不一,这类凹坑的形状是长条型或椭圆形,有时候也会出现圆形,一般固定位置单一,小编以前遇到过透过将喷水改为喷浆才使得凹坑有所改善的状况。
2、处理方法
针对这种凹坑,要检查喷水嘴的雾化状况,推荐用刀形雾焰的喷嘴代替圆锥形喷嘴,检查喷水后是否还有大点水滴滴在坯面上。
【更多相关介绍】
一、“凹釉”的定义及分类
“凹釉”也叫釉坑,成品釉表面可见到直径不等的圆形凹坑,因此可与印花粘网缺陷分开。一般发生在淋釉产品中,对于喷釉产品表面有油污时也会出现类似现象。
“凹釉”可分成两大类:
(1)物理型“凹釉”:一般过淋釉钟罩后可见,面积较大,数量不多,呈敞口状。
(2)化学型“凹釉”:过淋釉钟罩后不见,但烧成后可见,面积较小,数量较多,呈火山口状。
二、原因分析及解决措施
1、物理型“凹釉”
物理型“凹釉”主要由于釉浆中有油污或者坯体表面吸水率不一所造成。具体解决措施为:
(1)坯体原料配料球磨时混有树根、草皮和包装袋等有机质,素烧后坯体表面留有小坑,施釉以后釉浆沉落而构成凹陷,因此应在装球入料前尽可能除去这些有机质。一般小孔洞由于釉的表面张力没有影响,但直径大于2mm的孔洞则有此缺陷。
(2)粉料中间夹杂死料和结块等,致使成形时坯体致密度不一,从而使坯体表面吸水率不一。此时应稳定干燥塔的操作,防止出现堵枪或塌料状况,同时加强粉料过筛。
(3)粉料干湿度不一也会出现(2)所列的状况,此时应稳定干燥塔的操作,同时保证陈腐时间充足。
(4)成形时毛边脱落后被推入模腔中再次与粉料受压成形,其吸水率与正常粉料不一,一般成形后可见生坯表面有较深颜色的薄片。此时应改善模具结构,更换模具,同时加强高压气吹扫的操作。
(5)坯体表面粗糙,凹凸不平,釉浆依附于坯体表面构成凹凸不平效果。此时应调整粉料级配,同时选用硬质胶模或钢模。
(6)坯体表面受到破坏时也会产生如此缺陷。此时应调整扫灰刷子的压力,清洁推坯平台。
(7)坯体表面粘有坯粉时,素烧后粘粉处氧化烧成不足,导致吸水率不一致。此时应加强入窑前清扫坯表的工作。同时要注意窑顶落渣或爆砖也会产生类似影响。
(8)坯体表面在干燥窑和素烧窑中发生油渍污染,与釉浆相斥。此时应使烧嘴完全燃烧,防止油滴或油炭渣落在坯体表面。
(9)CMC质量不好或者变质发酵,也会影响釉浆质量。此时应选用优质的CMC,注意夏季高温时釉浆保存时间不能太长。
(10)在釉料的制备贮运过程中混入油质,尤其在换用釉泵管桶及搅拌机等新设备或在设备维修后应注意不要混入油污。少量的这种“凹釉”缺陷能够加入适量的洗洁精等来消除;若不能消除则要停止使用,换用新釉料,同时应注意检查釉浆放浆所用压缩空气是否混入油质。发生此类凹洞严重时釉面瀑布会开叉,一般很难消除,设备需要用洗衣粉大清洗,然后换干净釉药。
(11)施釉前喷水不均匀,甚至出现水滴,从而使坯体表面吸附釉浆不一。此时可采用刀形喷嘴保证喷水效果均匀。若用甩釉机淋水,则应提高其转速和加装甩釉塑片。
(12)釉浆中混入气泡,施釉于坯体表面后容易破裂构成“凹釉”。此时应保证釉浆足够的高度陈腐时间;釉桶中釉浆的高度不低于釉泵立柱上的射流孔,防止搅拌混入气泡;在钟罩上加装隔离筛网以除去气泡。
(13)施釉线工作环境不佳,灰尘漂浮,落到淋釉未干的釉面上。此时应加强施釉线清洁,同时多洒水。有条件的话,把施釉至印花段封闭,甚至把整个施釉线封闭避免灰尘漂落。此类凹洞在釉线上能看见凹洞中央有一个小杂质
(14)由施釉时施釉速度、淋釉重量和钟罩形状等造成,此时应调整淋釉工艺参数并使其稳定。
(15)目前喷墨印花产品,由于有些厂家的墨水油性较重,在做大墨量深色产品时,淋全抛釉时会有凹洞产生,此类凹洞需在淋釉前增加烘干装置,或者加印一道隔离剂
(蓝色字体为目前实际生产过程中比较容易发生的几种状况)
2、化学型“凹釉”
化学型“凹釉”主要由烧成时坯体釉层中发生的化学反应造成,一般生产中比较少见。具体解决措施为:
(1)在坯体配方中引入碳酸盐、硫酸盐等矿物较多,在烧成过程中受热分解所释放的气体冲开熔融釉层,尤其在坯料球磨筛余量较大时更加明显。此时应调整好坯体配方,降低烧失量;同时控制好泥浆筛余量。
(2)坯体原料中混有煤渣、铁质等,在烧成过程中与釉料发生反应。这种“凹釉”一般可见于凹坑中心处有黑色或绿色点状,因此应注意过筛除铁。
(3)干燥塔制粉时水煤浆燃烧不完全产生的煤灰混入粉料中,烧成过程中继续燃烧并放出气体。此时只能控制好热风炉,使水煤浆完全燃烧,并杜绝煤渣混入粉料。
(4)素烧时坯体氧化分解不完全,釉烧过程中仍有超多挥发气体,尤其大规格砖这种现象更加明显。此时应调整烧成曲线,延长氧化分解段。
(5)釉浆中有大颗粒杂质存在,烧成时反应异常,而该处釉料过少不能补平。此时应将釉料过100目筛才使用。
(6)熔块在熔制过程中反应不完全,气体未完全排除,在烧成时釉料发生第二次反应而造成。此时要求控制好进球熔块的质量,每批次熔块须做砖样实验。
(7)面釉的始熔温度太低,与坯体成熟温度不相匹配。此时可在面釉中适当提高高岭土的加入量。
(8)面釉的高温粘度大,表面张力不够匹配,熔融釉面不能拉平。此时应适当降低面釉的高温粘度。
三、结语
1、“凹釉”缺陷在水晶瓷片中比较常见,其产生原因涉及到釉面砖的每个生产工序,同时伴随有其它缺陷产生,需要时刻监测整个工艺流程。
2、“凹釉”缺陷在亮面瓷片较为常见,但其他釉面砖都会出现,只是个别哑光砖、仿古砖不明显看到。
3、在建筑陶瓷生产中,我们应加强分析各种缺陷的产生原因,准确快捷地解决生产中的实际问题,降低生产成本,提升质量档次。最重要的就是要能够准确决定产品凹釉的真正原因。
继续阅读与本文标签相同的文章: