相关推荐资讯
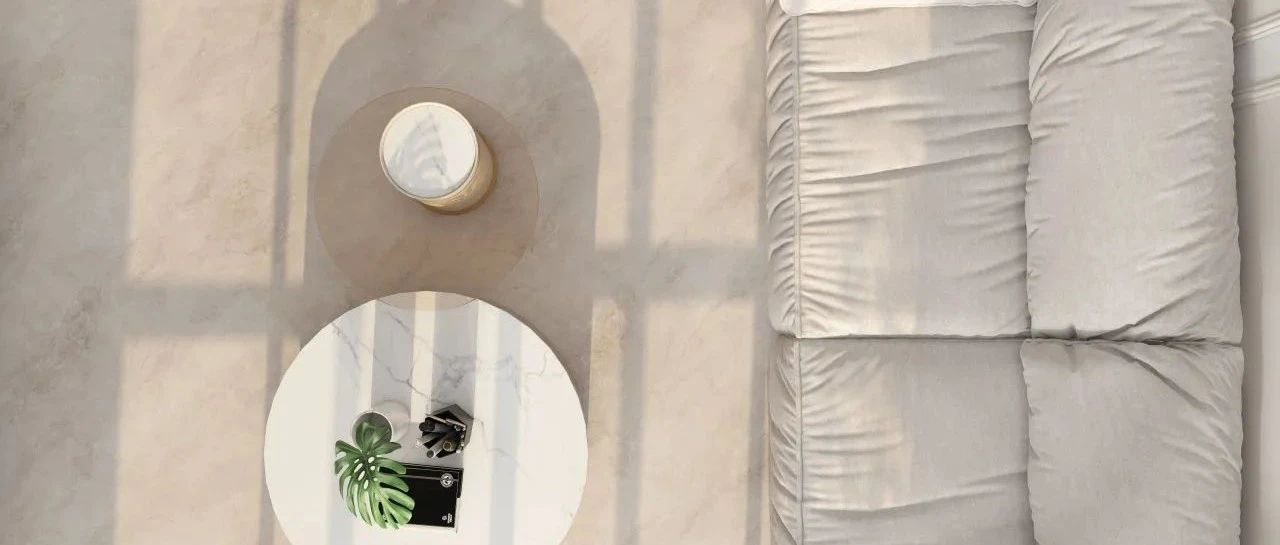
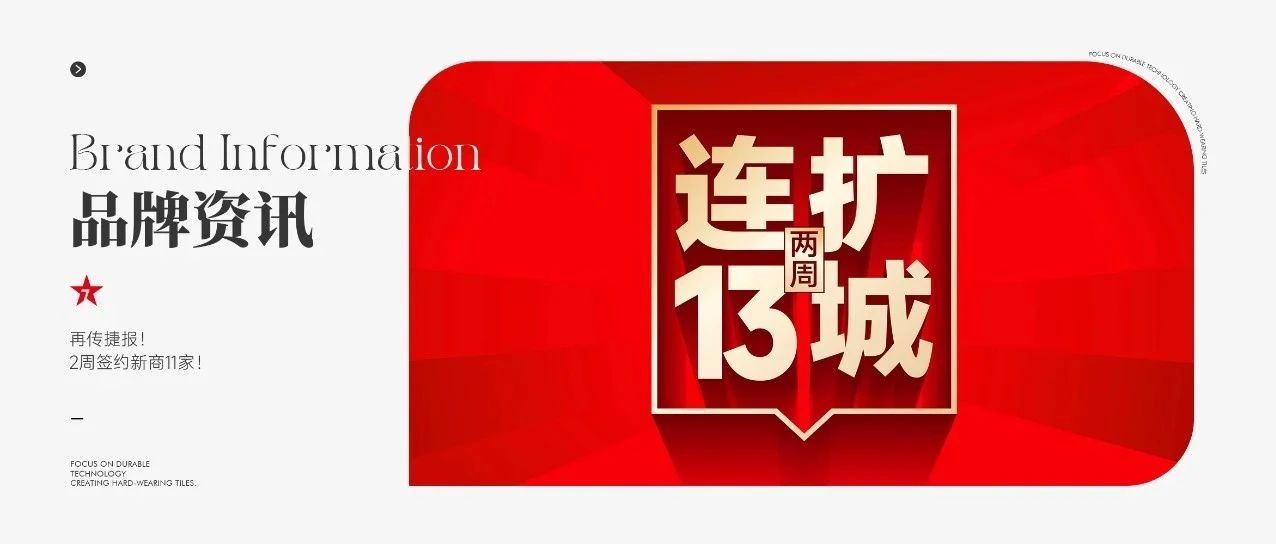
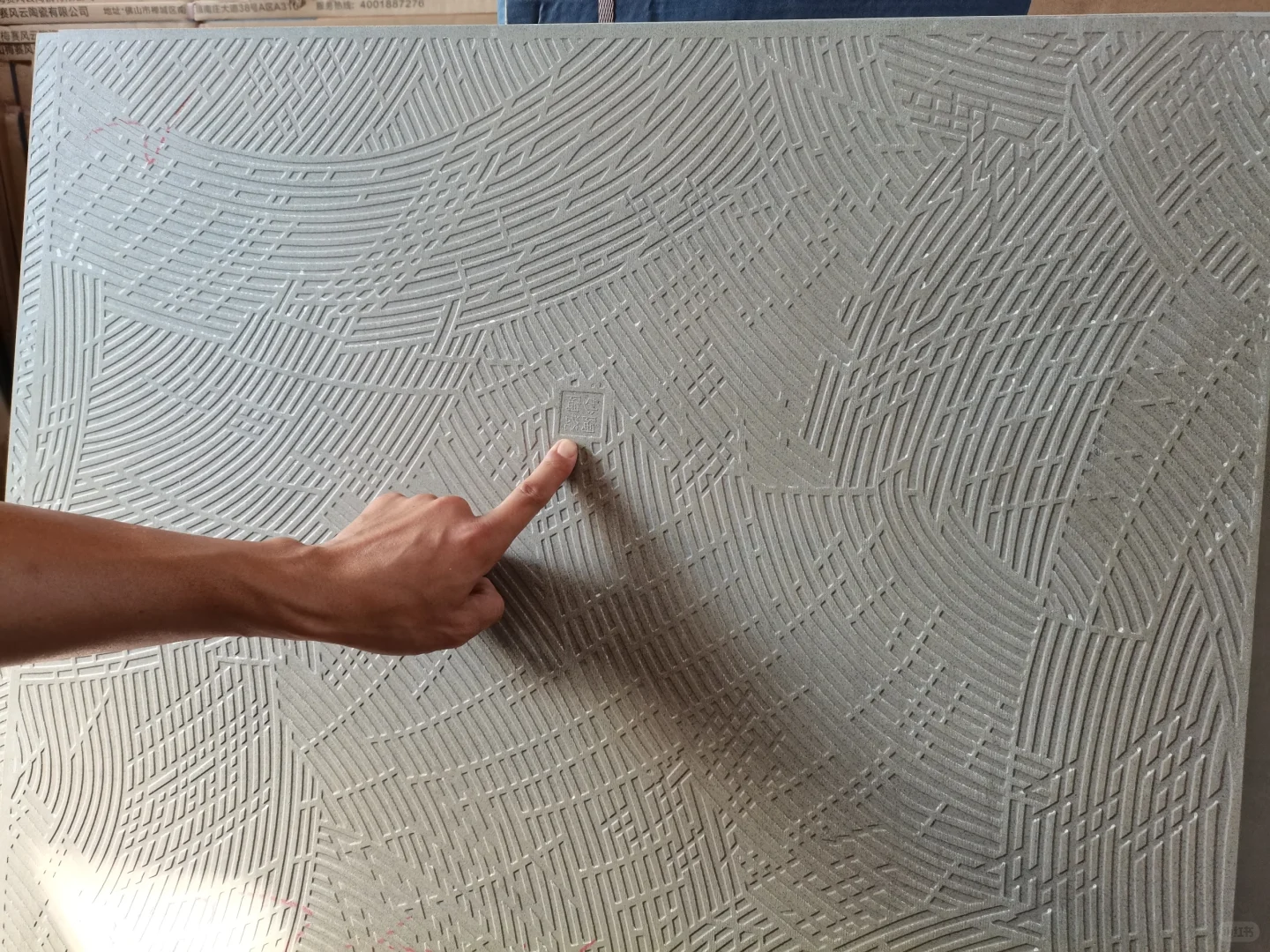
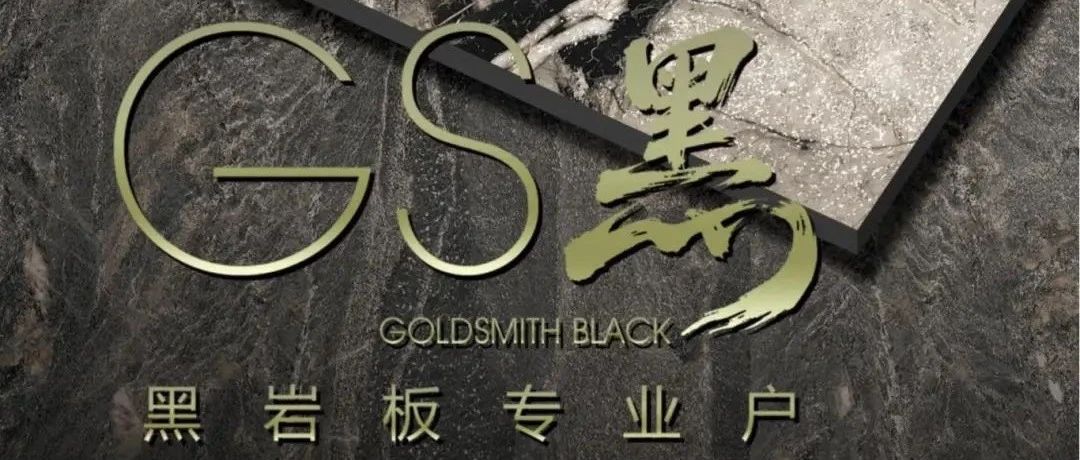
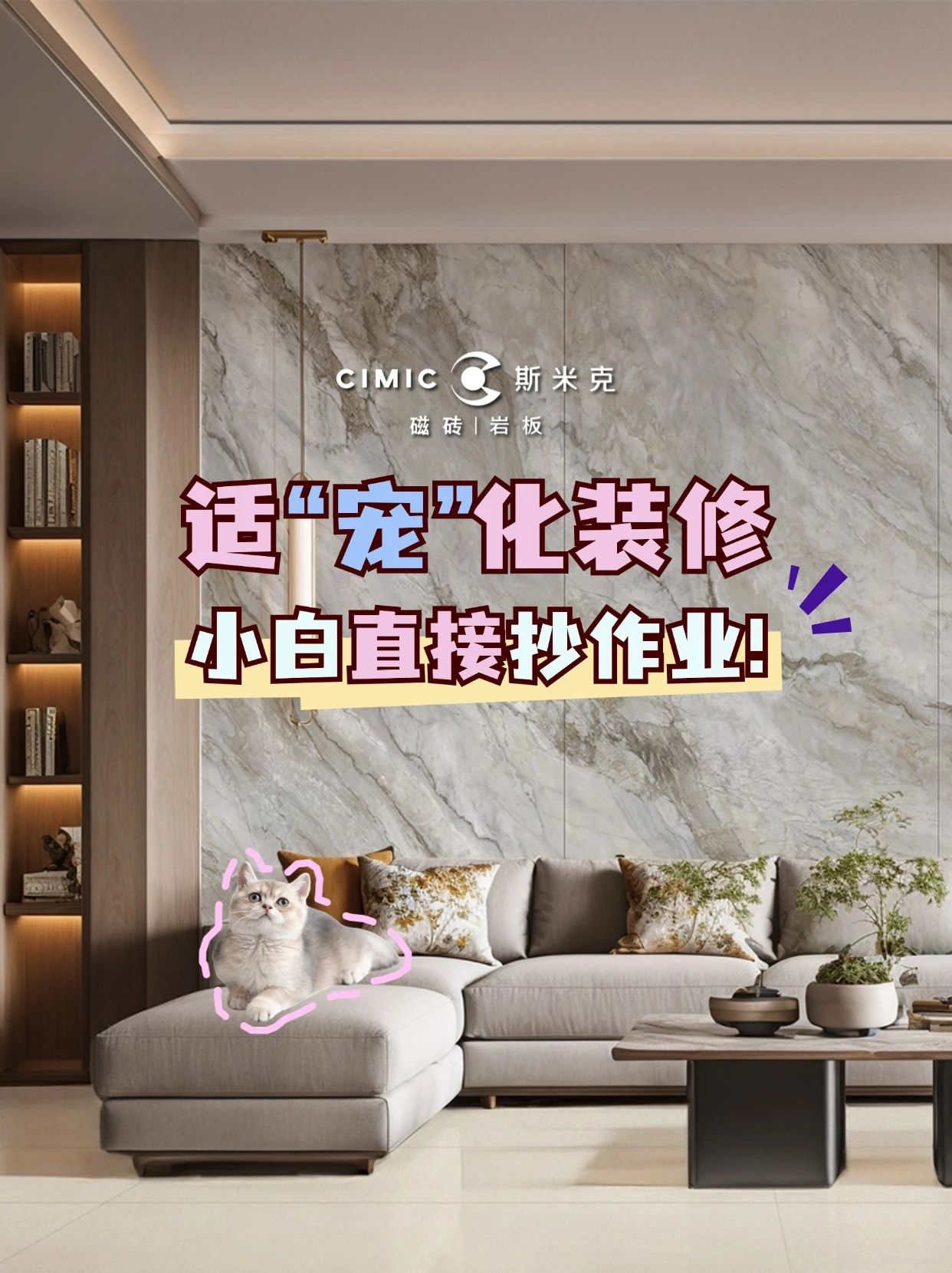
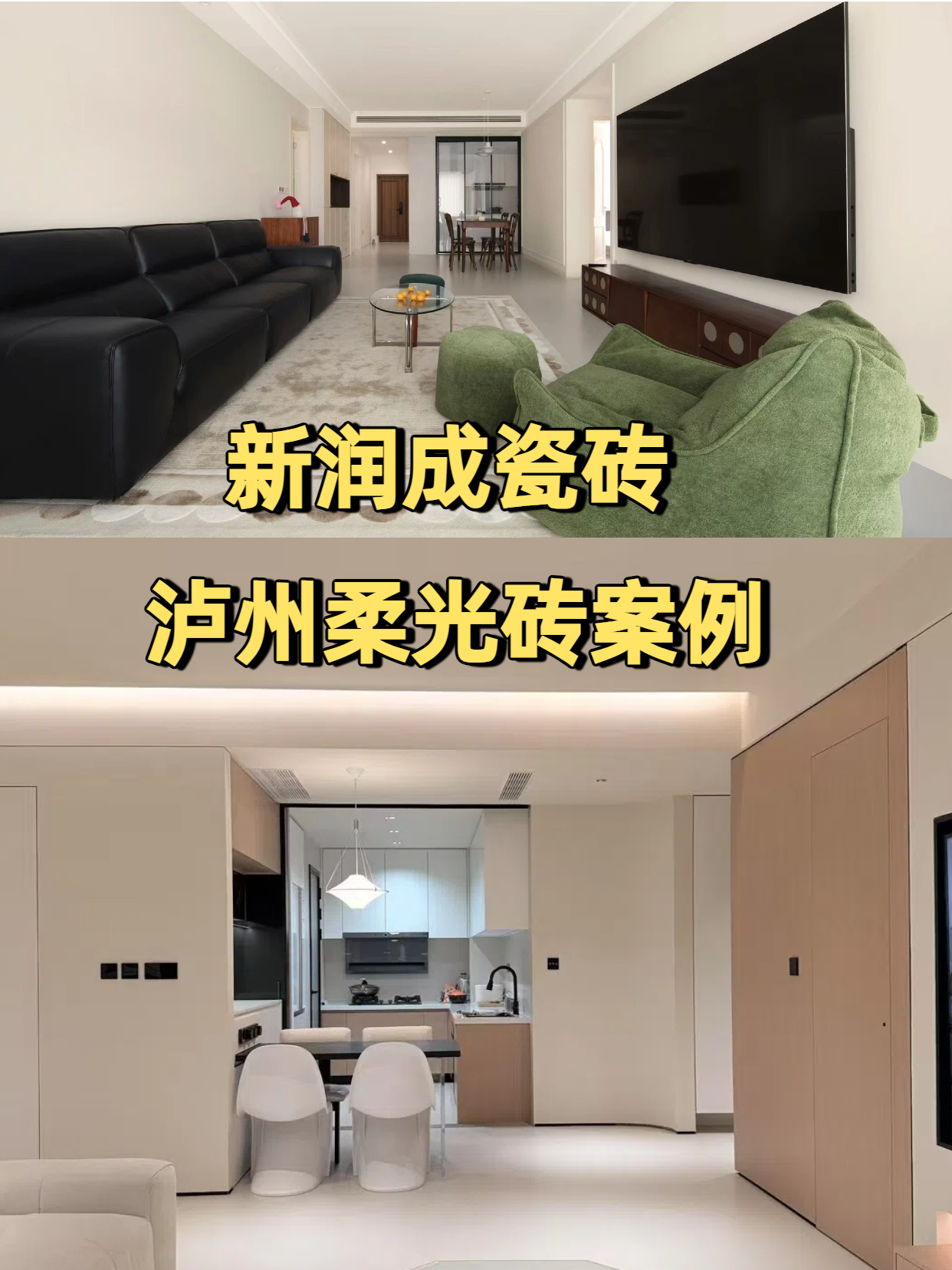
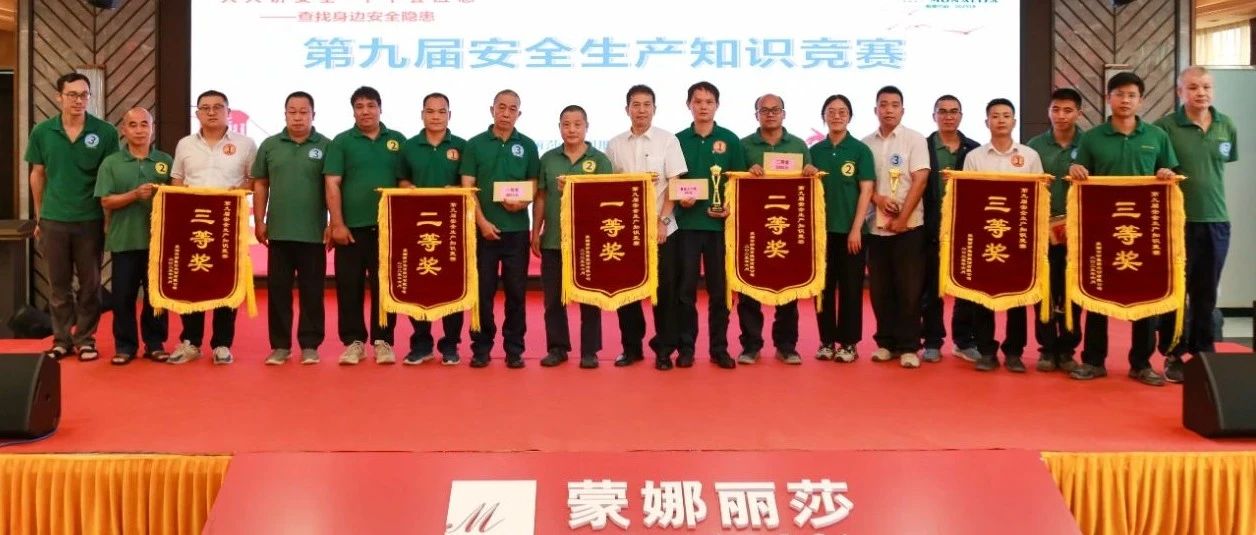
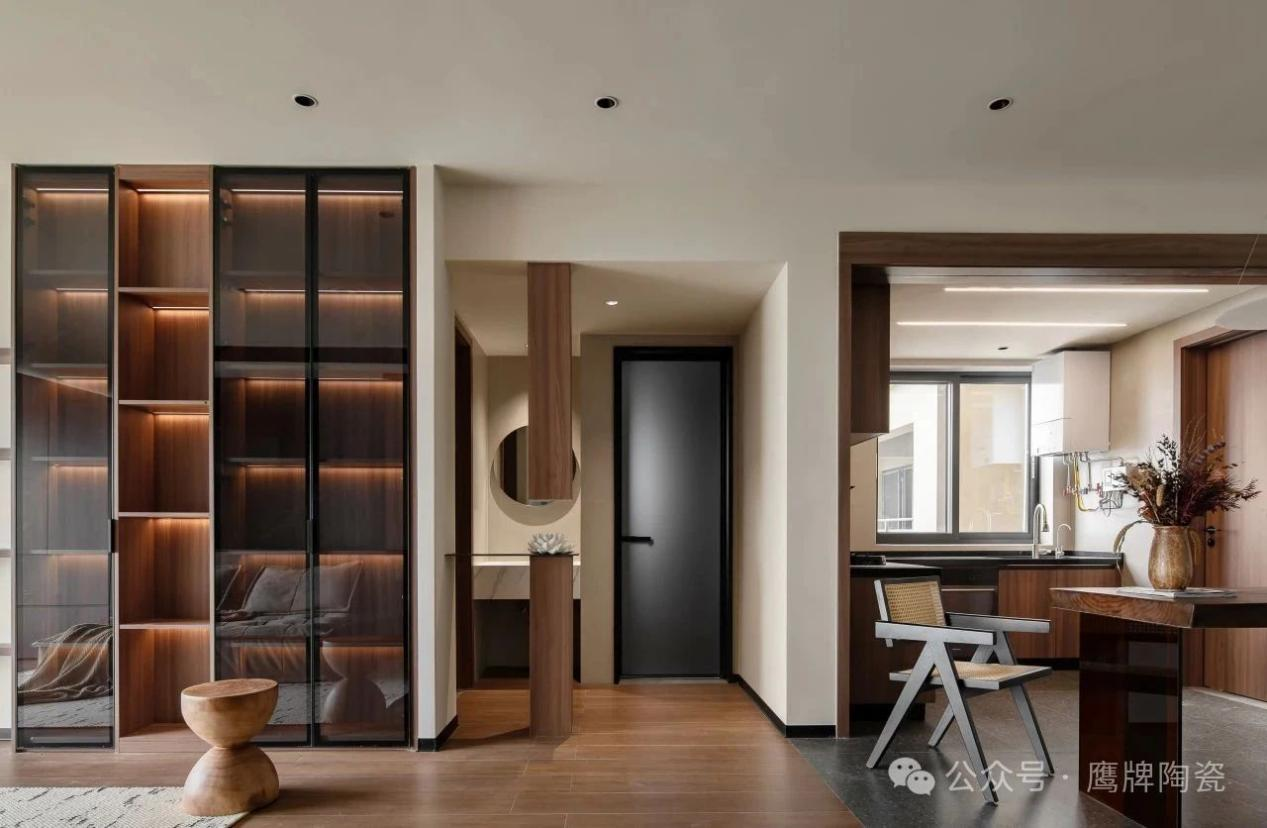
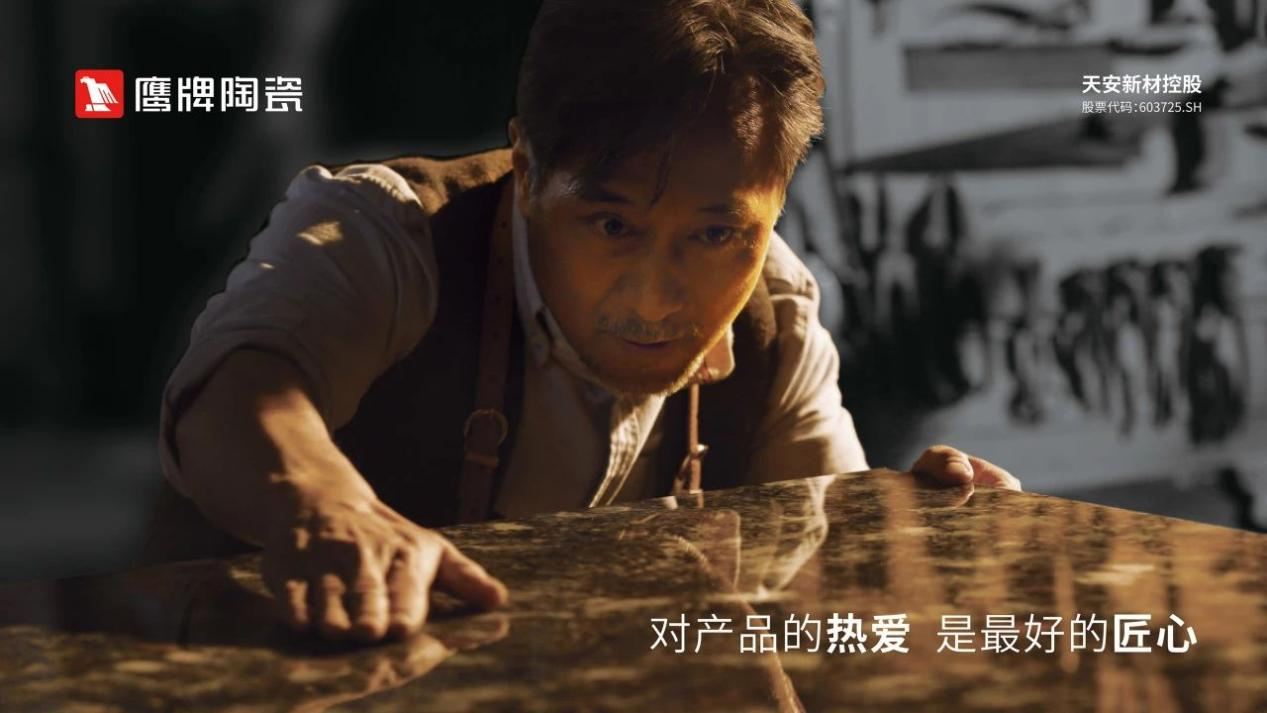
1、前言
我国是一个陶瓷墙地砖的生产大国。从1995年起产量突破15亿平方米的大关,1996年虽然略有下降,但仍然达到13.57亿平方米1997年甚至达到18.42亿平方米。针对建材业发展过程中生产过剩、价格下滑、结构失衡等弊端,今年起国家将实行“控制总量、调整结构”的战略目标。其中对建筑陶瓷提出的控制和调整目标为总量控制在10亿平方米以下,而高档产品占总量的比例要从目前的10%提高到20%-25%。
何谓高档产品﹖产品的内在质量好和外观质量好无疑是高档产品的必要条件,而陶瓷墙地砖是一种装饰为主要功能的产品,以前有人称为“陶瓷饰面砖”。因此,提高釉面质量,是提高陶瓷墙地砖外观质量和整个产品档次的重要途径和措施。
目前国内大多数墙地砖生产工厂,釉面点状缺陷(包括斑点、落脏、干洞、凹坑等缺陷)仍然是釉面质量进一步提高的主要困扰,特别是斑点、落脏等,一般占产品总产量的1-5%甚至更高。(一般工厂这项标准均以≤lmm,如果按高档产品的要求≤0.5mm则所占的比例会大大增加)
为了解决点状缺陷,最好的办法是从点状缺陷的分类及各类点状缺陷的形成原因以至机理分析入手,针对产生的原因和机理,对症下药,现将笔者工作中的点滴体会整理如下,仅供同行们参考。
2、釉面点状缺陷的定义及分类
2.1定义 点状缺陷是釉面出现的斑点、落脏、干洞、凹坑、棕眼等单个分布的缺陷的总称,是区别于色差、色脏等片状缺陷的一类缺陷。
常见点状缺陷术语
2.1.1斑点制品表面的异色污点。
2.1.2落脏釉面或产品表面附着的不同颜色且凸出釉面的异物。
2.1.8棕眼(又称针孔、毛孔)釉面出现的针刺样小孔。有的工厂把在釉面上的小孔称之为针孔。
2.1.4干洞施化妆土及面釉的产品,釉面出现的连接化妆土的较深的凹洞(也有工厂将这类连接化妆土的较深的凹洞称为棕眼)。
2.1.5凹坑施化妆土及面釉的产品,釉面产生的圆形下凹缺陷。本文分为冷态凹坑和热态凹坑。
2.1.6熔洞因易熔物熔融而让制品表面产生的连接坯体的凹洞,一般为较深。
2.1.7 滴釉由于施釉设备(一般为甩釉机)釉点下滴而形成的凸出釉面,与釉同色之缺陷。
2.1.8 釉泡釉面上可见的气泡(包括开口泡闭口泡)。
2.2 分类从生产实践中,点状缺陷可简略分类如下
2.2.1 按颜色分黑色、墨绿色、棕色、与釉同色。
2.2.2 按形状分圆形或近似圆形、不规则多边形。
2.2.3 按是否高出或低于釉面分凸出釉面、凹下釉面、与釉面平齐。
2.3 常见点状缺陷一般特征见下表:
当然,各个工厂工艺流程不同,设备水平有差异及环境不同,因此出现的常见点状缺陷的种类,比例各有不同,而且对这些缺陷的名称叫法也各不尽相同,这里为了讨论下文中问题方便,只能采用本公司的习惯叫法,仅供参考。
3、点状缺陷的产生原因和克服途径
3.1 斑点
3.1.1 产生原因
(1) 釉用原料中含有铁和铁的化合物、黑云母等
(2) 原料存放或加工过程中混入铁屑、铜屑、焊渣等
(3) 泥浆和釉浆除铁设施故障(如筛网破)或工艺失控(如溢浆等)未能除尽铁质和杂质
(4) 环境不好,半成品表面,落有异物,而人窑时未清理干净
(5) 燃料含硫量过高,烧成时与铁质化合而生成硫化铁;
3.1.2 克服途径
(1) 釉用原料要进行精选,每种原料进厂必须要经过检验,使用成釉的工厂必须有一套有效的检验程序
(2)改善原料存放,加工过程的环境和设施,尽可能减少存放和加工过程中混入铁屑、铜屑及其他杂质
(3)完善泥浆、釉浆的除铁设施和工艺,特别是要注意控制浆料经过除铁装置时的流量,不能太大,触变性不能过高
(4)对含硫量较高的燃料要进行脱硫处理
(5)在施釉后,釉面还未干的坯体要加以防护,不让脏物落在未干的釉面上窑前应装一负压吸尘装置或吹灰风机,不让半成品表面的脏物进人窑炉。
3.2 落脏
3.2.1 产生原因
(1)贮釉桶中落入杂质
(2)半成品施釉存放,运送过程中,特别是釉面未干之前落入脏物,入窑之前未能清除
(3)储坯车,窑具上的脏物粒子落在釉坯表面,而入窑之前又没有及时清除
(4)窑顶上的耐火砂浆,釉料的挥发物和风管上的脏物落在制品表面
(5)助燃风机的吸人口的过滤设备失效,吸人脏物
(6)砖坯与砖坯之间相互挤在一起,把一些容易碰落的小结构碰下来,而通过气流作用落在刚好熔融的表面上,例如有一种叫SPACER的凸缘砖(每边有二个凸耳)就很容易造成这类落脏。
3.2.2 克服途径
(1)改善釉浆的管理,出浆及施釉之前釉浆要过筛,必要时要加大筛的目数,有些工厂曾经用到150目以上
(2)施釉后釉面未干的产品要加防护设施,防止落入脏物
(3)车间的生产环境要好,在同一车间内几条生产线生产的喷釉,施云彩机一定要有吸尘罩,防止色点落在其他生产线的釉面上。云彩机、甩釉机施完釉后,一定要将护罩等冲洗干净、防止生产下一批产品时落下色点
(4)如用储坯车,要定期清理。窑具要经常涂氧化铝,(如果用窑具的话)陶辊磨后也要涂上涂料。
(5) 定期清理窑吊顶、窑墙、风管。检查助燃风机吸入口除尘装置。
(6) 烧制带凸缘的spacer类产品时,要注意砖与砖之间在釉料的高温熔融阶段,砖坯不要挤得太紧,并要调整窑内的压力,使辊上的压力尽可能大于辊下压力。如果是负压,要让辊下的负压的绝对值大于辊上负压绝对值。
3.3 棕眼
3.3.1 产生原因
(1) 釉的始熔温度过低,高温粘度过高。
(2) 熔块熔化不透,夹有生料。
(3) 化妆土保水性差,使施面釉时渗水过急,坯体空隙的气体排出过急,突破釉面而形成小孔,而釉面高温粘度较大又来不及熔平。
(4)施釉时坯体温度过高,过干或喷水过少,使釉浆渗透坯体的速度过快
(5) 施釉前未将吸附在坯体表面的灰尘杂质等清除干净
(6) 预热带氧化段的辊下温度过低,坯体和釉料中含有较高温度下才分解氧化排出气体的杂质,气体未完全排出,釉层已开始封闭
(7) 烧成温度过高,釉面过烧,出现小针孔。
3.3.2克服办法
(1) 调整面釉配方,适当提高釉的始熔温度,降低高温粘度
(2) 提高熔块熔化质量,选择质量好的熔块
(3) 改善化妆土的保水性,适当增加保水性较好的原料,如增加优质高岭土、球粘土的含量,也可以适当增加添加剂或粘结剂的含量,如CMC,VC-All9(阿米索罗)
(4) 保证施釉后,坯体未干之前釉面的清洁
(5) 调整并控制好烧成温度,特别是预热带氧化段的温度,使一些需氧化的物质在釉面始熔之前就氧化完全,气体提前排出
(6) 分别试验配方中各种原料在900℃以前和1200℃前的烧失量,如果发现某原料后期烧失过大,及时采取补救措施(预烧)和更换
(7) 适当降低烧成温度或提高面釉的成熟温度范围。
3.4 干洞
(1) 立式干燥窑调节不当,或者由于施釉线停止时间过长,以至施釉前坯温过高喷水量又没有及时调整,以至使坯体施化妆土时温度过高,施完化妆土后肉眼就可看到小孔
(2) 化妆土的粘度过大,带入气泡不易排除,保湿性不好,粘结性不好,坯温高时收缩过快
(3) 面釉的釉浆性能不好,粘度过大,气泡不易排除,保水性不好,收缩过快
(4) 喷雾塔中积聚的干粉集中在一起,没有经过陈腐均匀,在坯体中形成收缩不均匀区
(5) 坯体,化妆土的原料不纯,有在较高温下分解的杂质
(6) 喷水与化妆土之前的距离,施釉与施化妆土之间所设位置不当
3.4.4 克服途径
(1) 立式干燥器要及时调节,让出坯坯温稳定、均匀(一般不超过90℃),增加坯温红外线自动连续测量和显示装置,并根据坯温的升高及时调节喷水量,最好能根据坯温自动调节喷水量
(2) 改圆锥形雾焰的喷嘴为刀形雾焰喷嘴
(3) 控制化妆土浆的性能,严格控制细度、流速、比重、保湿性、粘结性、必要时用球粘土、CMC、PC-67和VC-All9(阿米索罗)进行调整
(4)控制面釉的细度、流速、比重、保湿性、粘结性能,必要时用CMC,PC-67,VC-All9进行调整
(5)改变化妆土的施布方法,例如改为淋化妆土
(6) 喷雾干燥生产过程中应清除从排风管塌下来的干粉,对新喷出的粉料一定要陈腐24小时以上才能使用
(7) 通过化学分析调整配方,更换原料、清除坯料、釉料、化妆土中的高温下分解的物质
(8) 正确调整从喷水到施化妆土,从施化妆土到施面釉的距离。
3.5 凹坑
建议将凹坑分为冷态凹坑和热态凹态。
冷态凹坑指施完釉后肉眼就可见到的凹坑。
热态凹坑指施釉之后肉眼不能看见,而烧成后才能看见的凹坑。
3.5.1 产生原因分析
(1) 原料、釉料、化妆土中带有低熔点物质,配方中添加CMC或STPP等比例不当。粒度分布过粗或粗细不均匀。
(2) 喷雾干燥风管落下的干粉集中在一起没有清除,压型后引起坯体局部收缩不匀。
(3)喷水、化妆土、面釉及添加剂中及压缩空气中有油污染。
(4) 喷水不均匀或喷水后有水滴在坯体表面,引起局部吸收化妆土或面釉不好。
(5) 化妆土或釉浆中有气泡不易排除。
(6) 施釉线上的大环境不好,空气受粉尘或其他物质(例如印花之前固定釉面的胶水)微粒污染,在釉面没有干燥之前落入尘埃或橡胶屑等
(7) 面釉中的CMC变质、发酵、施面釉后就出现冷态凹坑
(8) 面釉始熔温度低,高温粘度大,化妆土的烧结温度过低,烧成时气体排出之后来不及熔平产生热态凹坑。
3.5.2 克服之途径
(1) 加强进料检验,防止低熔点物质混入
(2) 粉料一定要经过24小时以上陈腐,让喷雾干燥后的粉料水分均匀,电解质晶体分解,假颗粒分散开,干粉粒吸入一定水分
(3) 检查储釉、化妆土、面釉之容器,搅拌机、输送和喷水、喷釉之压缩空气中是否有油污,必要时加适量的洗洁净、万洁灵分散之
(4) 检查喷水嘴的雾化情况,建议用刀形雾焰的喷嘴代替圆锥形喷嘴。检查喷水后是否还有大点水滴滴在坯面上
(5) 施釉(淋釉、甩釉(打点))后的产品,在釉面未干之前要设防护罩。要有专人检查施釉后有没有落脏。发现环境不好,要及时纠正,制作高亮釉的车间内所有的喷釉、喷胶水装置都必须装吸尘装置,防止外逸。
(6) 热天要防止面釉中的CMC变质可采用现磨现用,缩短使用周期的办法,或者将面釉存放在阴凉处,或在面釉中加入防腐剂。
(7) 适当提高预热带的坯温,提高面釉的始熔温度和化妆土的烧结温度,使气体排出后釉面能及时熔平。
3.6 熔洞
3.6.1 产生原因分析
(1) 粉料、釉料化妆土运输过程中带入杂质及粉料、釉料、化妆土中存在低熔点物质,在过筛中又未能除去,在没有施化妆土的面釉中使面釉局部熔点降抵,引起较深的熔洞
(2) 喷雾干燥粉料陈腐时间不够,电解质、燃烧不完全物和其他物质分布不均匀或吸附在铁点和其他带色金属一起发生作用,引起带色熔洞
3.6.2 克服途径
(1) 严格粉料最后一道过筛,防止大粒低熔点杂质混入
(2) 控制喷雾干燥粉料的陈腐时间,最好达到24h以上,让“聚集”在一起的铁点、电解质颗粒和其他低熔点物质分解
(3) 泥浆筛控制在100目以上,遄釉筛控制在120-150目,化妆土筛控制在180目。
3.7 滴釉
3.7.1 产生原因
(1) 甩釉机没有按规定时间及时清洗
(2) 釉浆的触变性过大
3.7.2 解决途径
(1) 定时清洗甩釉机
(2) 调整釉浆的触变性
3.8 釉泡
3.8.1 产生原因分析
(1) 坯料中含有较高温下分解的有害杂质的原料过多
(2) 釉料中含硫酸盐、碳酸盐、有机物过多或含过量的碱性氧化物
(3) 釉料的始熔温度过低,高温粘度高,使坯体分解出的气体无法顺利排出
(4) 坯体中混入碳粒、胶屑、机油等有机物
(5) 施釉时釉浆粘度过大,“包裹”有大量的气体并汇集于釉层中
(6) 由于釉浆流动,釉料中的可溶性盐聚集在坯体的边缘处
(7) 烧成曲线不合理,预热带升温过急或烧成温度过高。
3.8.2 克服途径
(1) 减少坯料中较高温分解产生气体的原料的含量,用低灼减量的原料取代
(2) 调整釉料配方,提高始熔温度或降低高温粘度
(3) 改善粉料加工、存放、输送的环境和设备,防止有机物混入
(4) 制釉时先把可溶性盐类制成熔块,熔块水淬后应充分水洗
(5)改进施釉方法和操作
(6) 调整和控制好烧成曲线,预热带氧化段的温度可适当提高,氧化气氛可适当增强。
继续阅读与本文标签相同的文章: